Top Strategies for Effective Reverse Logistics in 2025
Reverse logistics refers to the process of handling returned products, including activities like returns management, refurbishing, and recycling. Efficient reverse logistics can reduce costs and improve customer satisfaction. In this article, we will explore key strategies and technologies to optimize reverse logistics for businesses.
Key Takeaways
- Reverse logistics is essential for minimizing costs and enhancing customer satisfaction by efficiently managing returns, refurbishing, and recycling.
- A solid reverse logistics plan is crucial for companies; it not only cuts down on return costs but also improves the overall customer experience.
- Technology, automation, and data insights play a significant role in optimizing reverse logistics processes, leading to better efficiency and sustainability.
A reverse logistics expert explains that the process of reverse logistics involves transporting items from consumers to their origin, be it manufacturers or sellers.
In contrast to traditional logistics that centers on delivering goods to customers, reverse logistic operations go in the opposite direction and encompass tasks such as managing returns, refurbishing products, recycling materials, and reassigning leased equipment.
Effective management of reverse logistics is crucial for cutting expenses, diminishing waste output, and improving customer satisfaction. It necessitates detailed planning and organization to manage the backward movement of goods competently.
Key Differences Between Forward and Reverse Logistics
The fundamental difference between traditional logistics and reverse logistics is the flow of goods. Traditional logistics orchestrates the movement of products from manufacturers to customers, whereas reverse logistics begins at the customer end and involves transporting items back to retailers or producers.
In contrast, while traditional logistics focuses on distributing products and managing inventory effectively in order to fulfill consumer demand, reverse logistics deals with processing returned items with an aim to extract value by means of refurbishment, recycling, or resale. Acknowledging these contrasts is essential for proficient management of reverse logistics and enhancing overall supply chain efficiency.
Importance of a Solid Reverse Logistics Plan
Having a strong reverse logistics strategy is essential for success in the current competitive environment. It helps to lower the costs associated with returns and improves customer experience by ensuring that returns are processed quickly and efficiently. By establishing an effective system, waste can be decreased, which enhances overall supply chain performance.
Implementing an effective reverse logistics approach preserves revenue, augments customer lifetime value (LTV), and alleviates pressure on customer support staff by reducing their burden.
How Reverse Logistics Works
Reverse logistics is the process of recapturing value from products that have been returned by employing effective methods like returns management, recycling, refurbishing, and reselling.
These strategies are critical across different sectors, but hold particular importance for ecommerce companies due to their considerable influence on profit margins through the management of returns.
Dealing with defective or unwanted items requires arranging transportation, conducting inspections and tests, performing repairs or processing for recycling. A strong reverse logistics system not only bolsters conventional supply chain performance but also focuses on sustainability efforts. The use of advanced software solutions can greatly enhance efficiency in these operations.
Steps in the Reverse Logistics Process
The reverse logistics process starts with customers returning products. A clear returns policy and procedures guide how returns are initiated. Once returned to the warehouse, products are examined for restocking, repair, or disposal based on their condition.
Efficient returns management maintains customer satisfaction and financial health. Returned products are categorized as perfect, discounted sale, donation, or defective products.
Reverse logistics providers quickly assess the condition of returned merchandise, while standardized data collection on return reasons refines the process.
Role of Technology in Reverse Logistics
Implementing advanced technology infrastructure significantly improves the effectiveness of reverse logistics. An integrated IT system elevates the ability to monitor and track returned merchandise, along with utilizing software that can streamline procedures, expedite product restoration, and boost overall operational performance.
The employment of automation along with artificial intelligence plays a vital role in monitoring and evaluating reverse logistics processes to enhance efficiency as well as customer interactions. Systems providing instantaneous insight into operations coupled with tools for managing inventory guarantee competent management of returns. AI augments the consumer experience by diminishing the need for numerous support contacts while favoring exchanges rather than reimbursements thereby preserving sales revenue.
Types of Reverse Logistics Processes
Reverse logistics encompasses a variety of processes such as managing returns, remanufacturing, and recycling, all essential components for a robust system. Efficiently managing the return of products is key to boosting customer satisfaction within returns management, and remanufacturing plays an important role by refurbishing returned items to near-original quality for resale, which is vital for recapturing value.
In terms of sustainability, recycling handles packaging materials in a way that minimizes waste and supports the development of a circular economy.
Returns Management
Clear return policies are essential for efficient returns management, enhancing the process and elevating customer satisfaction. These policies focus on reducing returns by implementing rigorous quality control measures and facilitating the initiation of returns in an effective manner.
When products are returned, they undergo evaluation to determine if they can be restocked, repaired or need to be recycled. Top e-commerce companies implement accurate inventory management systems to minimize mistakes and consequently decrease the frequency of product returns.
Remanufacturing and Refurbishment
The remanufacturing process revitalizes products, making them comparable to new items by adhering to stringent quality and performance criteria. This procedure includes taking apart, cleansing, and putting the product back together.
On the other hand, refurbishment incorporates modern technology into previously returned goods so that they comply with contemporary benchmarks prior to being resold. These methods are crucial in renewing products to a state similar to newness, prolonging their product life cycle, and enhancing the recovery of value from these items.
Packaging Management and Recycling
Managing packaging sustainability diminishes the amount of waste produced and encourages the recycling of materials. By reprocessing packing materials, it is possible to decrease both waste and contamination, thereby conforming to eco-friendly procedures.
The implementation of a circular economy model reduces waste by advocating for product repurposing and material recovery. It focuses on prolonging the life span of products through tactics such as reuse, repair, and material reclamation. Reverse logistics supports these efforts by allowing for the mending and recycling of products that would otherwise be thrown away.
Benefits of Implementing Effective Reverse Logistics
Implementing an effective reverse logistics strategy can lead to reduced operational expenses and increased profits. By smartly managing the reverse supply chain, businesses are able to convert it into a source of profit through cost containment. Such efficient frameworks diminish financial losses associated with product returns, thus bolstering profit margins.
Businesses that employ tactics such as refurbishing items that have been returned can significantly improve their customer experiences. The adoption of successful reverse logistics not only cuts down on costs, but also heightens consumer satisfaction, setting the stage for enduring business expansion.
Cost Reduction
An efficient reverse logistics system lowers transportation and administration costs, creates value by turning waste into sales, and reduces storage and distribution costs. Optimized systems improve financial outcomes, customer retention, and supply chain visibility.
Digital tracking systems manage product lifecycles and improve recovery rates. Proper packaging management reduces shipping costs by optimizing materials. Partnering with experts refines the supply chain, saving time and money.
Enhanced Customer Satisfaction
A seamless return process boosts customer satisfaction and encourages repeat purchases. A strong return policy enhances retention and satisfaction rates. &Collar, for instance, improves customer satisfaction through Redo, leading to enhanced satisfaction and efficiency. The process returns are designed to boost customer loyalty and be user-friendly.
Optimized reverse logistics processes retain customers by ensuring a smooth and satisfactory return experience.
Environmental Sustainability
By adopting sustainable reverse logistics strategies, companies can minimize waste and support environmental protection efforts by aiming to decrease carbon emissions within the supply chain. Such an emphasis on sustainability encourages firms to adopt greener practices.
Current movements in reverse logistics are geared towards improving recycling processes and implementing methods that lead to a reduction in waste.
Common Challenges in Reverse Logistics
The growth of e-commerce has increased the complexity and costs of reverse logistics. Companies focus on minimizing disruptions caused by returns. Future developments will prioritize minimizing these disruptions.
Enhancing return processing by interconnecting all aspects is another key role that is equally important.
Handling Delivery Failures and Return Fraud
Return fraud can cause substantial financial losses, sometimes billions annually. Relaxed return policies can exacerbate these losses, making effective fraud prevention essential.
Retailers increasingly use sophisticated methods and AI technologies to detect and combat return fraud.
Managing Excess Inventory and Unsold Goods
Returning unsold products is often driven by inventory becoming obsolete. Implementing clear strategies to handle this surplus stock can lessen the monetary consequences. Permissive return policies may exacerbate problems related to having too much inventory.
Having an abundance of stock that exceeds demand can lead to significant financial setbacks for companies.
Infrastructure and Technology Integration
To manage reverse logistics effectively, it is imperative to have the correct infrastructure and software in place. The two-way movement of goods demands suitable infrastructure. Consistent oversight and assessment are crucial for maintaining efficient logistics operations.
Strategies to Optimize Reverse Logistics
Effective coordination between returns and inventory management minimizes costs. Cohesive policies can significantly differentiate a company’s approach to handling returns and repairs.
Businesses can drastically enhance their reverse logistics efficiency through effective coordination and clear policies.
Streamlining the Return Process
Optimizing the returns process necessitates having straightforward policies and providing effortless access to various shipping alternatives. Employing automation solutions such as Redo can elevate the customer experience by streamlining both reverse logistics and interaction.
Take &Collar, who employed the Redo platform to refine their returns process, which led to a quicker return workflow and improved experiences for customers. Firms are able to cut expenses by limiting the number of returned items through strategic use of technology and integrating reverse logistics with regular distribution processes.
By entering into negotiations with carriers about return shipping rates, businesses have an opportunity to trim costs significantly, thus lowering their aggregate shipping expenditures. Facilitating a user-friendly online returns procedure reduces time spent on customer service interactions while boosting overall operational efficiency.
Leveraging Data Insights
Leveraging data insights and real time insights optimizes reverse logistics processes. E-commerce retailers use advanced analytics to understand return patterns and adjust inventory management accordingly. AI technologies enable faster and more cost-effective return processes.
Analyzing return data refines product design and minimizes future returns. Data analytics identify trends and support informed decisions in reverse logistics management.
Partnering with Reverse Logistics Experts
Working together with experts in reverse logistics can lead to increased efficiency and cost reduction when handling product returns. ReverseLogix is an expert in the supply chain, focusing on fixing products and recovering assets. Applications such as Reveni and Dawa simplify the return procedures by enabling immediate refunds and mechanizing requests for Return Merchandise Authorization (RMA).
Bigblue offers a technological platform dedicated to managing returns as well as outsourced logistics services, which improves overall business operations. Meanwhile, ReturnGo collaborates closely with shipping companies to facilitate more efficient return logistics. Companies are advised to carefully assess the features of each system in order to select the one that best matches their needs.
Real-World Examples of Successful Reverse Logistics
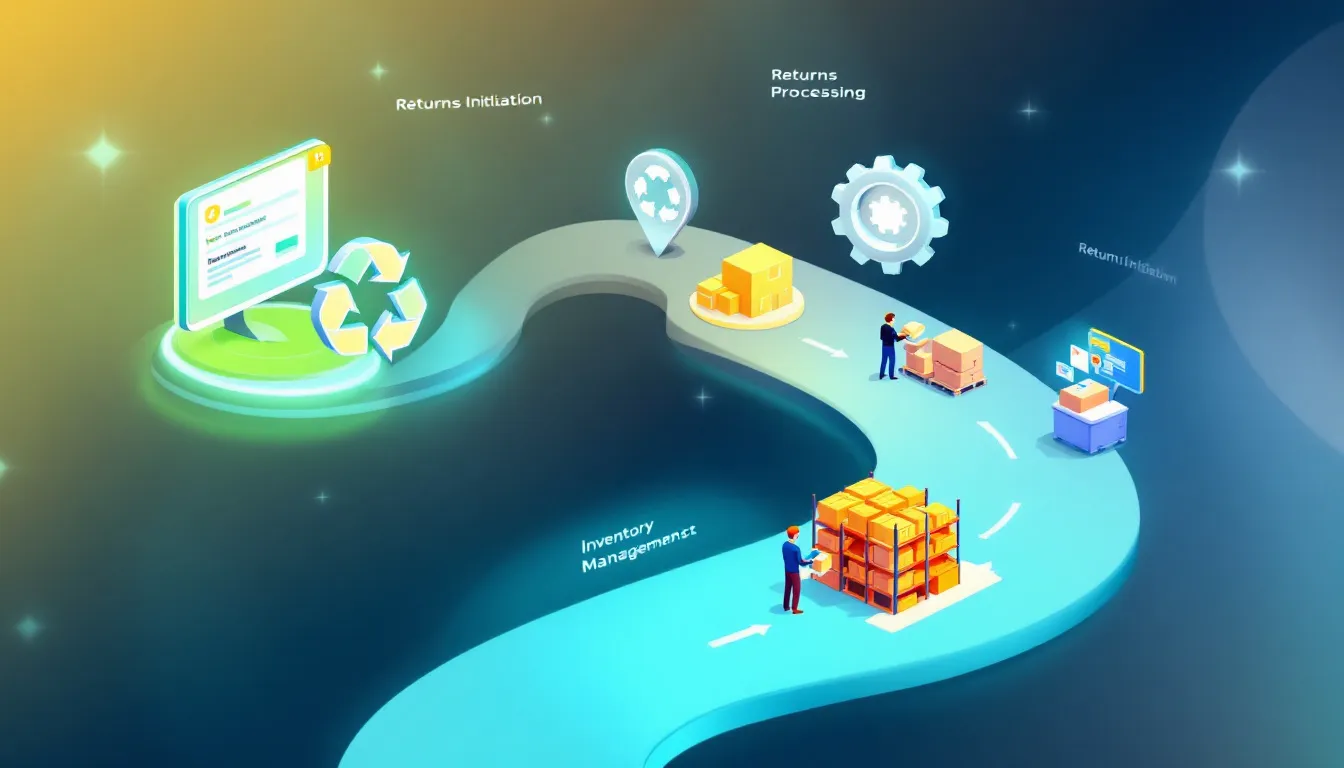
Real-world examples of successful reverse logistics illustrate the impact of effective strategies. Home Depot allows customers to return online orders by mail or store drop-off, facilitating efficient logistics. Kohl’s partners with Amazon to manage returns, making the process convenient and attracting customers to its stores.
Companies like Amazon and Zappos have optimized their return processes, significantly enhancing customer satisfaction through efficient reverse logistics. Levi Strauss enhances sustainability by repurposing jeans and reprocessing fibers to create new products, showcasing innovative reverse logistics.
Proctor & Gamble and Unilever have shifted to reusable packaging, allowing consumers to return containers for cleaning and reuse products.
Case Study: &Collar's Experience with Redo
The incorporation of the Redo app into &Collar’s operations has significantly transformed their business, leading to satisfied customers and mutual benefits. The process of integrating Redo with their existing system was remarkably straightforward, enhancing communication and streamlining the returns procedure for Shopify orders. This improvement has not only pleased customers, but also reduced the workload for businesses.
With an impressive 93% of its reviews being 5 stars, store owners are expressing high satisfaction with Redo due to its easy-to-navigate interface and attentive customer service team. By offering a comprehensive suite of premium products through one unified platform, Redo eliminates the hassle associated with handling various applications separately. It delivers uncomplicated warranties that have garnered positive reactions from consumers.
Innovative Practices in E-commerce
Ecommerce businesses are adopting technological advancements to make return procedures more efficient, which in turn enhances customer experience and bolsters consumer loyalty. Outvio is revolutionizing reverse logistics by optimizing these processes and transforming returns into an additional sales channel.
The implementation of cutting-edge practices within the scope of reverse logistics is critical for ecommerce entities aiming to handle returns with greater efficiency. By integrating innovative technologies within their reverse logistic strategies, these companies achieve higher levels of customer satisfaction as well as enhanced operational performance.
Future Trends in Reverse Logistics
Integrating sophisticated supply chain management software is key to the evolution of reverse logistics, streamlining operations and increasing efficiency. The incorporation of robotics and artificial intelligence within reverse logistics is improving productivity while simultaneously decreasing expenses related to labor.
By unifying every element involved in the returns process, businesses can refine their approach to handling returns, thereby reducing any interruptions caused by returned goods within the supply chain.
Integration with Circular Economy Models
Top e-commerce companies are adopting initiatives aligned with the circular economy, urging consumers to send back products for recycling and lessen their ecological footprint. These measures assist businesses in cutting down on waste production while fostering sustainable habits among shoppers.
The concept of the circular economy advocates for identifying alternative purposes for discarded items via processes such as reclaiming, fixing up, and repurposing materials.
Advances in Automation and AI
Automation and robotics are emerging as key trends in reverse logistics, helping companies manage returns more efficiently while reducing labor costs.
The integration of AI in reverse logistics enhances customer experience, reduces support touch points, and increases the likelihood of exchanges over refunds, retaining revenue.
Increasing Focus on Sustainability
Companies are increasingly acknowledging the significance of implementing sustainable practices within reverse logistics to diminish their ecological footprint. Levi Strauss exemplifies this by recycling old jeans and extracting fibers that are then used in the production of new denim garments.
Incorporating sustainability into reverse logistics can involve measures such as material repurposing, engaging in recycling processes, and endeavoring to minimize waste. These actions contribute to a reduced environmental impact and often garner favorable reception from environmentally conscious consumers.
Summary
Reverse logistics is no longer just a supplementary part of the supply chain; it is a critical element that can drive cost savings, enhance customer satisfaction, and promote sustainability. From understanding the basic principles to exploring advanced strategies and real-world success stories, it is clear that effective reverse logistics management is essential for modern businesses. Implementing a solid reverse logistics plan can mitigate high costs, improve customer experiences, and contribute to environmental conservation.
As we look to the future, the integration of technology, the adoption of circular economy models, and the increasing focus on sustainability will continue to shape the landscape of reverse logistics. By leveraging data insights, streamlining return processes, and partnering with reverse logistics experts, businesses can turn potential logistical challenges into profitable opportunities. Embrace the power of reverse logistics, and transform your supply chain for a sustainable and efficient future.
Frequently Asked Questions
What is reverse logistics?
Reverse logistics is all about managing the flow of goods back from consumers to manufacturers or sellers, including things like returns, recycling, and refurbishing.
It’s a key process for maintaining sustainability and efficiency in business.
Why is a solid reverse logistics plan important?
A solid reverse logistics plan is key because it can help lower costs, boost customer satisfaction, cut down on waste, and streamline your supply chain.
It’s an investment that pays off in multiple ways!
How does technology impact reverse logistics?
Technology significantly improves reverse logistics by enhancing tracking and visibility of returns, streamlining processes through automation, and boosting operational efficiency with AI.
These advancements make handling returns smoother and more effective for businesses.
What are some common challenges in reverse logistics?
Managing delivery failures and combating return fraud, along with handling surplus stock and incorporating technology efficiently, are common problems encountered in reverse logistics.
Tackling these obstacles is essential to ensure smooth operations and achieve customer satisfaction.
How can businesses optimize their reverse logistics processes?
To really optimize reverse logistics, focus on streamlining returns, using data insights to inform decisions, and teaming up with experts in the field.
This approach can boost efficiency and cut costs significantly.